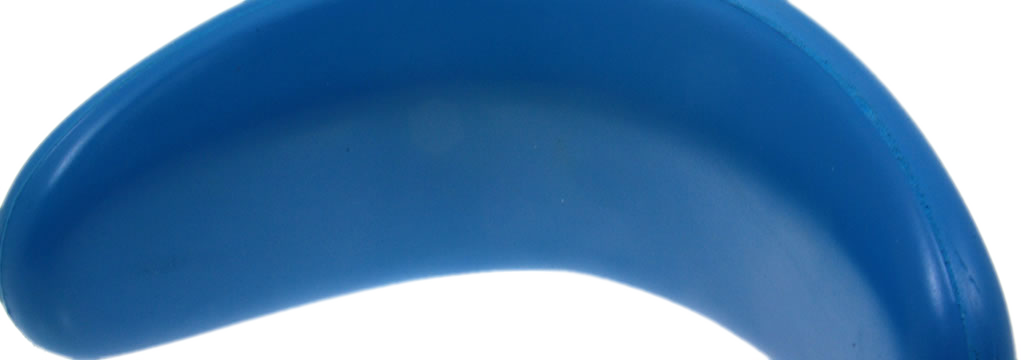
Integral Skin Foams
Integral Skin Foam or “self skinning foam” usually comprise of a low density foamed core with a high density skin of the same material. This is achieved in a single moulding operation, where the foaming material forms a much tougher skin on impact with the contours of the cold mould.
The process is used in many applications including vehicle interiors, furniture components and leisure goods. The moulded components can easily encapsulate armatures (inserts) made from other materials as well as fixings and finishes such as bolts, Velcro strips or steel strengthening parts.
Advantages
- Lightweight, flexible core with tough exterior
- Low tooling / prototype costs
- Excellent shock absorbing properties
- Good abrasion and chemical resistance
- Excellent noise insulation properties
- Good dimensional stability
- Components can be RFI shielded
- Additives can be used for flame retardants, UV stability, colour and anti-microbial needs
- Various Densities and Hardness giving varied mechanical and physical properties
Typical polyurethane material specifications
Elastomer | Elastomer | Flexible PU foam | Structural rigid foam | Structural rigid foam | Insulation foam | |
Moulded properties | CG9 9026 72D | CG9 9007 70A MF | IS DP6252ZM | Isofoam RM 509W | Isofoam RM 522W | – |
Hardness , Shore A | – | 70 | 45-75 | 96 | – | 160 |
Hardness , Shore D | 72 | – | – | 42 | 54 | – |
Thermal Conductivity (Wm-1 K-1) | – | – | – | 0.05 | – | 0.03 |
Tensile strength (Kpa) | 20 | 7 | 1370 – 1375 | 5700 | – | – |
Elongation (%) | 26 | 215 | 75 – 109 | 4.3 | – | – |
Tear Strength (N/nm) | – | – | 5.3 – 5.45 | – | – | – |
Burn characteristics (mm/min.) | – | – | <100 | – | – | – |
(Estimated values for reference only)